Selecting, specifying, applying valves & actuators for optimum system performance
Valves and actuators may not be the largest pieces of equipment in a system, but they do have a considerable impact on energy efficiency.
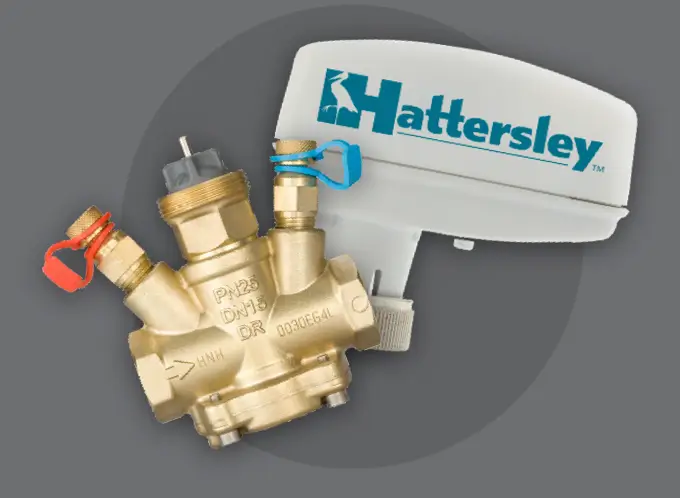
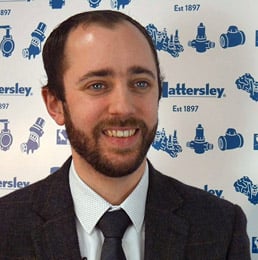
In this feature, Neil Gibson, Hattersley Technical Manager for UK and Ireland, discusses the factors to consider when specifying valves and actuators, including issues such as testing and sizing.
He also offers advice on how to ensure valves and actuators work in harmony to deliver more comfortable indoor environments that are also energy efficient in the long term. And how this pairing can also support other important areas such as preventative maintenance to help the facilities management team.
Hidden gems
Valves and actuators are largely unseen elements of a building services system, but as Neil Gibson explains, they can have a significant impact on system performance, occupant comfort and energy efficiency.
Despite pressure independent control valves (PICVs) being in the market for almost 20 years, it is only in the last 5 to 10 years that we have seen a significant uptake in their use. As a result, there has been a relatively short period of time for specifiers and installers to gain and in-depth understanding of their use and function.
Hydronic systems, which use water as the medium for transferring heat, must be in balance. Any imbalance leads to overheating or over-cooling; causes discomfort for building occupants; and wastes energy. In the past, the main type of hydronic system contained a constant volume of water, with 3- or 4-port control valves with constant speed (low volume) pumps to control the heat output of the terminal.
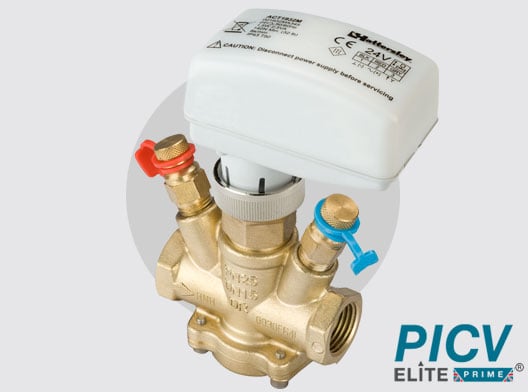
The benefit of this approach is easy sizing of control valves. But the constant volume approach means that water is being pumped around a system even when there is no demand. And this in turn leads to areas of discomfort (temperatures too hot or too cold) for occupants as well as energy waste.
With the move to more energy-focused system design, variable volume systems have come very much to the fore. They deliver heat only when it’s needed. The challenge is that achieving and keeping balance in the system means using three pieces of equipment: a differential pressure control valve (DPCV); a 2-port control valve; and a balancing valve. This means the system is more complex to design and time-consuming to install.
However, the pressure independent control valve (PICV) is capable of making the variable volume system much easier to design and manage. It combines all three functions in a single technology. Design is much easier, and PICVs make installation and commissioning more straightforward. As their use has become more widespread, it is now acknowledged that PICVs greatly assist in the efficient and effective operation of heating and cooling systems.
There are a number of characteristics to consider when selecting and sizing a PICV for a project. Accuracy of control is vital for a balanced hydronic system, so flow control and flow rate are the first points to check. Flow setting is another important aspect. The valve should be easy to set by hand for commissioning purposes. The latest PICVs offer quick-fit actuator connection with no tools required.
Due to the wide range of flow rates available within PICVs it is often possible to select a valve at a smaller pipe size than requested, which is still capable of achieving the required flow rates in an efficient manner. This can subsequently help in reducing capital expenditure for the project
The minimum pressure required to activate the PICV can vary between sizes and setting so this is also something to think about. Pressure drop across the PICV can vary between valve sizes, about 15kPa for smaller sizes increasing to 30kPa for larger valves. An increased pressure drop in the least-favoured circuit could increase the whole-life operating costs of the system.
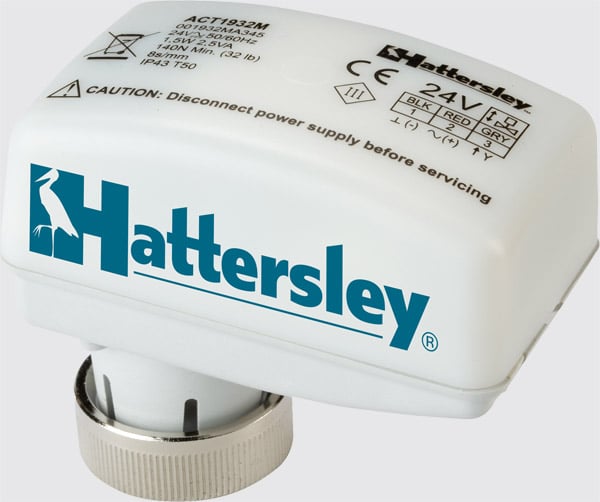
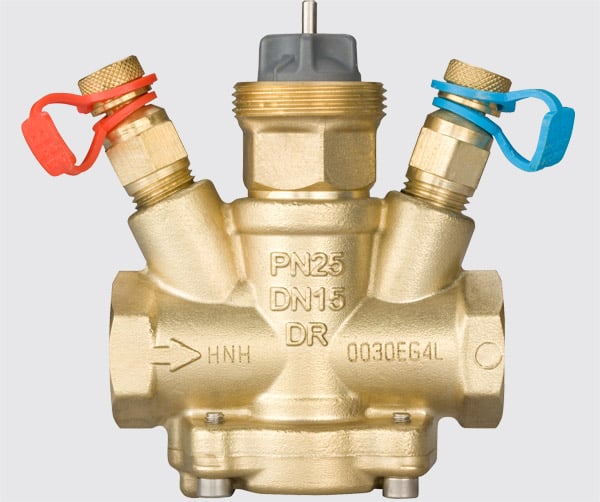
Another important factor to bear in mind is that a PICV and an actuator should be thought of as a matched pair. A PICV matched to an actuator provides a more responsive heating and cooling system, which means people are more comfortable, and a stable room temperature will optimise energy efficiency.
The actuator is designed to meet the required closing force and stroke length of the valve. Gap detection allows the actuator to detect the reduced stroke setting of the valve. This ensures maximum valve authority is maintained – allowing for quicker response to demand changes in the heating and cooling system.
A feedback signal is also a useful function to consider. This allows users to monitor the exact actuator position. A variation in the signal during operation could indicate that the valve or actuator could require attention soon. This means that the feedback feature could be viewed as a tool for preventative maintenance.
Of course good installation practice is vital to ensure that the PICV and actuator perform as required. Best practice is that the pipework components that have a relatively high-pressure drop should be installed in the return pipework. This reduces the risk of cavitation – the formation of bubbles in the liquid.
The installation of pressure test points is recommended at various positions. This makes maintenance easier, as well as verification of system operation and other trouble shooting.
As the PICV is set to give a specific flow rate, there is no commissioning of the valve required, beyond flow rate verification. However, the commissioning engineer does need to set the pump speed to ensure the PICV has sufficient pressure available to ensure it is in working range.
Making the right choice of PICV is important. Their increased use has brought more of these products onto the market but it’s fair to say that not all PICVs are created equal. When considering which valve to select, it is sensible to ask about the level of testing applied to the product at the design and production stages. For example, Hattersley has its own manufacturing and testing facilities so we can carry out testing on our products from the design stage to production, before they leave our factory. This allows for 100% pressure and performance testing on each PICV manufactured in the UK.
Our tests conform to a number of industry standards including BTS01 and the BSRIA flow limitation test, which assesses a PICV across the full differential pressure rating of the valve to ensure that it performs as described by the manufacturer. We can also test at elevated pressures beyond those required by standards; sometimes upwards of five times the rated pressure.
The PICV is a very useful tool for energy efficiency in today’s buildings. With careful selection and consideration of some basic factors, they can provide a highly cost effective backbone to a robust and efficient heating and cooling system.